Wire harness processing flow and process requirements
Wire harness processing is a precise and complex work. In order to ensure the quality of wire harness products,
the wire harness processing process generally needs to be standardized and standardized.
Usually, the process of wire harness processing can be divided into the following steps:
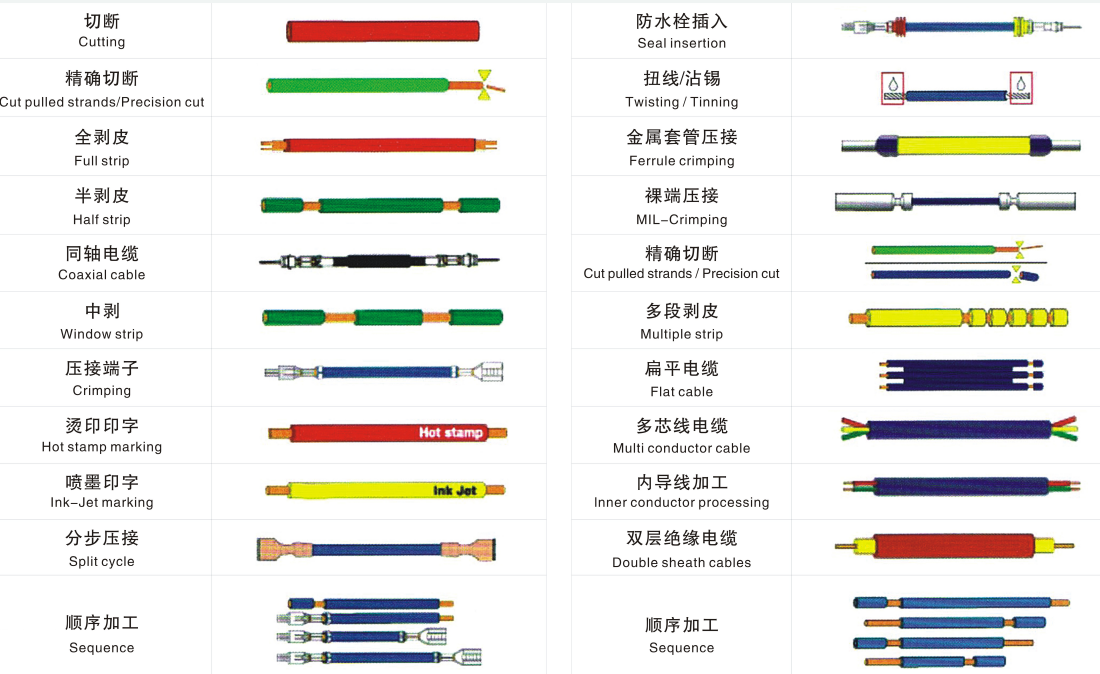
1. Wire delivery
Wire feeding equipment: Put the required processed wires on the intermediate wire feeding frame.
Required equipment: wire feeder, wire feeder.
Process requirements: Be careful not to scratch or scratch the surface of the wire. Avoid different wire tightness when multiple wires are processed at the same time
2. Cutting
Cutting line: use the cutting machine to cut the wire to the required length
Required equipment: computer wire cutting machine, multi-function wire cutting machine, wire cutting and stripping machine.
Process requirements: Do not cut the surface of the wire; Do not cut the copper wire; The error of the length of the peeling is not allowed to exceed +1mm.
3. Peeling
Wire stripping: According to the requirements of SOP, strip the insulation jacket of the corresponding length of the wire at the joint. Required equipment: Wire cutting and stripping machine, vertical stripping machine, pneumatic stripping machine Process requirements: Do not crush the surface; The error of stripping length is not allowed to exceed + 1mm.
4. Twisted wire
Twisted wires: Arranging and twisting the conductors at the joints
Required equipment: Cutting, stripping and twisting machine, cutting and twisting machine.
Process requirements: no scratching or scratching the surface of the wire; the copper wire must be twisted tightly, and loose wires are not allowed
5. Crimp terminal
Riveting terminal: Rivet the conductor at the joint and the plug terminal. Required equipment: terminal machine, single and double-head terminal machine, automatic terminal machine, copper strip machine, silent terminal machine. Process requirements: the terminal is not deformed and must meet the requirements of tension, riveting height and width
6. Dip tin
Tin dipping: tinning the joints to facilitate the insertion of circuit boards. Required equipment: automatic tin dipping machine, single and double-head tin dipping machine, cutting line tin dipping machine.
Process requirements: tinning is uniform, no loose wires are allowed, and the depth of tin dipping meets the requirements
7. Assembly: Assemble the plastic plug shell
Required equipment: electric screwdriver.
Process requirements: the screws are not allowed to expose the surface of the plastic shell; the torque required by the product must be met.
8. Conductivity test: use the instrument to conduct the continuity test of the wiring harness
Equipment needed: Continuity tester.
Process requirements: short circuit, open circuit, miswiring, poor contact, poor insulation and other phenomena are not allowed.
9. Packaging: Use plastic bags to package the finished wiring harness and put them in cartons
Required equipment: sealing machine and packing machine.
Technological requirements: the seal should be flat;
FAQs
Are you looking for a reliable manufacturer of down home textile products?
We can quickly provide customers with market analysis, technical support and customized services.subscription
Please send your message to us
- *Name
- *Tel
- *Title
- *Content